We bought our first 3D Printer and had a massive learning experience!
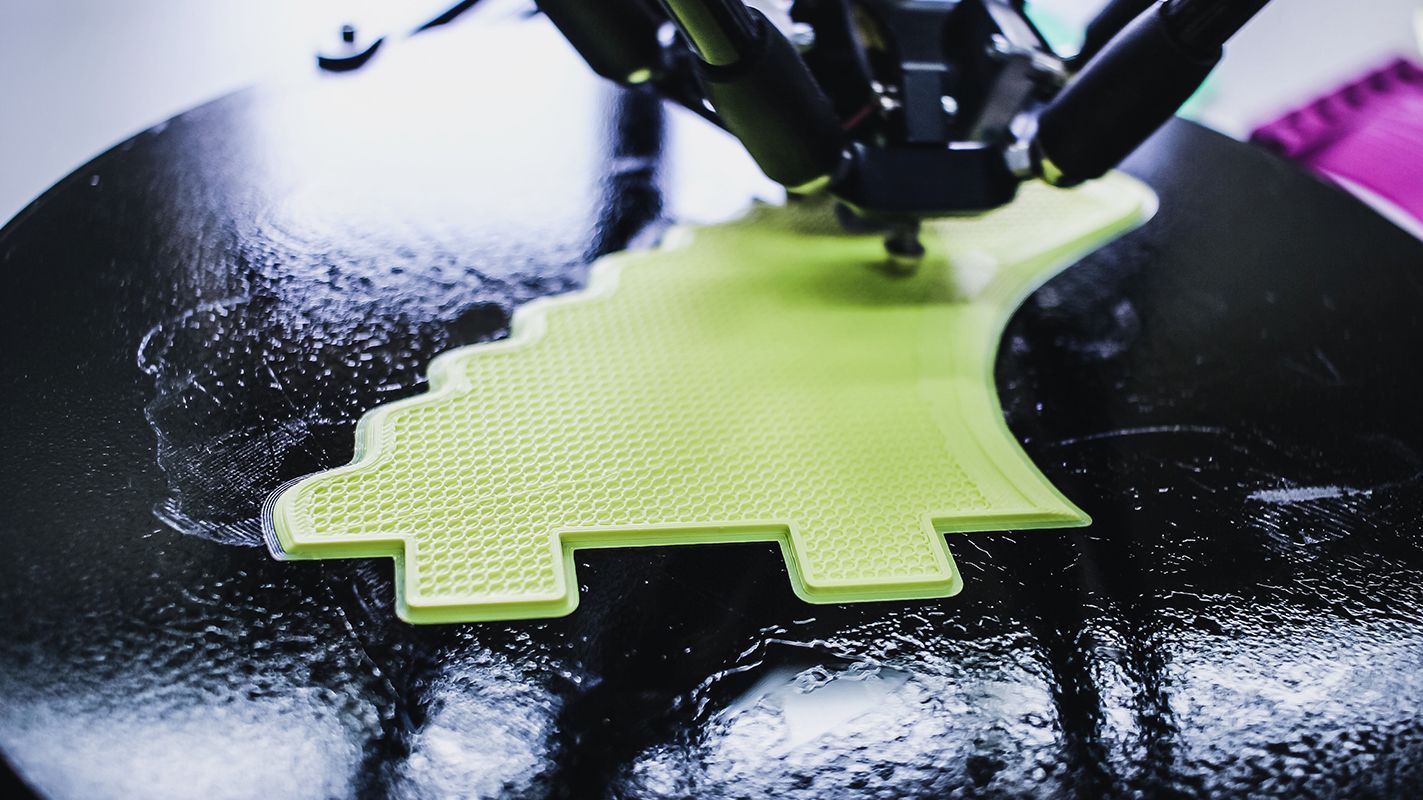
A few weeks ago my wife asked me for a 3D printer. She wanted to make art and small things around the house. Two weeks ago we spend a whole evening researching and comparing 3D printers and design software. It turns out to be quite an adventure and we learned a lot along the way.
In this post I will take you through our first steps into the wonderful world of 3D printing and show you how we got our first 3D printer.
Choosing a printer
You can get a 3D printer for about 200 euros, but you can also get one for about 2500 euros. There are some pretty big differences between the various printers you can buy.
When we started looking into printers we quickly learned that a 3D printer is not something you buy, assemble and use straight away. A 3D printer is a device that you have to tinker with to get perfect results. Everyone we talked to replaced about 60% of the parts of their 3D printer after one or two years.
With that information in mind we decided on a few requirements:
- We want to use our printer for building a RC-car with a raspberry PI mounted on it. This means it should print decent sized components. The printer should be able to build objects in the range of 20-30 cm in all directions.
- We were prepared to spend some money on this. 400-600 euros was no problem for us. We already knew that the cheaper printers produced lesser quality prints, so we didn't want to go cheap.
- Since we discovered that a 3D printer is a device that you need to tinker with, we wanted something without a case. We wanted to be able to replace parts easily.
I think it's good to think about what you need before you get a 3D printer. One other tip that is important, get a printer that produces decent quality prints, but don't spend all your money on your first printer.
Rolf, a colleague of mine said to me: You will definitely get a second printer. So I wouldn't go too big or too expensive on the first one. It's best to use your first printer as a prototype/experiment to learn the basics of 3D printing.
Setting up a tool chain
While researching 3D printers, tools and materials we learned that in order to print any 3D object you need a few tools on your computer too.
There are two pieces of software you need:
- A 3D design tool to build the objects you want to print.
- A slicer, which converts your 3D design into a file that is readable by the printer.
- A tool to manage the printer itself.
3D design software
There are quite a few options when it comes to 3D design software. The choice of 3D design software depends largly on what you want to make.
Art is typically made with sculpting tools, but replacement parts and every day objects are made with parametric design tools that require you to specify exact dimensions.
Also, some tools are easier to use than others. There are tools for beginners, which help a lot with the design process, but limit what you can make. Of course on the other end of the spectrum there are product design tools that are really complicated, but also offer maximum flexibility.
We found a comprehensive list of tools online that has almost every tool you can imagine on it.
We decided to give Fusion 360 a shot. We've seen a lot of makers on youtube use it and noticed that they had a lot of fun using it.
Fusion 360 is certainly not the easiest tool to use, but there are some pretty good courses on pluralsight. Since we both have a subscription for pluralsight, we decided to watch the online courses for Fusion 360 to learn how to use it.
Once we watched the first course on pluralsight we were able to design a few basic objects. Not all of them are printable I think, but I guess we'll find out.
Slicer tools
As I mentioned before, you need a slicer tool to convert your 3D designs into printable designs. A slicer tool will convert the object into layers and then write a GCode file with all the instructions for the 3D printer.
The GCode format is universal to all 3D printers, so it doesn't really matter which slicer tool you use.
What does matter is how ergonomic the slicer tool is. You want something that really helps you turn your design into a GCode file.
There are a few things that are important:
- The tool should have a good set of defaults for your printer. Because there's a lot to configure in terms of layer size, temperature of the nozzle, temperature of the bed, printing speed and about a gazilion other options, you want something that is good enough by default. A good slicer tool helps you with that.
- The tool should allow you to rotate and place the object on the printer bed, so you can design in any orientation and then reorient the object in the slicer, so it prints in the optimal direction.
- 3D printers don't handle overhangs very well. It simply can't print floating layers. You have to add supports for overhanging parts. You can do this manually, but a good slicer helps you do that.
We ended up downloading cura from Ultimaker. It's a tool that has a nice user interface.

There are of course other slicer tools, but we haven't tested them at all. Here's a list of tools that we discovered while researching:
Integration between the different tools in your tool chain
One cool feature that we found really useful is the Make button inside Fusion 360. It allows you to send 3D objects from Fusion 360 directly to your Slicer utility. In fact, if you use a tool that integrates with Fusion 360 you can print your objects straight from the design tool.
While not necessary, we found that having the design tool integrate with our slicer made the whole 3D print process a lot smoother.
Use a printer management tool
You can connect your printer via USB to your computer. Some slicer tools can send the GCode instructions directly to your printer this way. Another method to get your sliced model to the printer is to put it on an SD-card and place the card in the printer.
We started out using the SD-card that came with the printer, but learned that it wasn't the easiest method of printing.
One problem is that you have to walk up to your printer to see the progress of your printer. Our printer is on the top floor of our house and typically, prints take a few hours to complete.
Edwin, another colleague of mine told me about a tool called Octoprint. This tool can be installed on a raspberry PI. You connect the printer to the Raspberry PI and octoprint will manage your printer for you.
Octoprint has a web interface which allows you to monitor the printer from your couch on your iPad, laptop or other device. It gives you a complete overview of the printing process.
Also, Octoprint can access webcam devices on your PI. So we put up a camera next to the printer so we can see what's going on. No more surprises when the filament gets tangled, or the print fails, or whatever else can go wrong.
This is just the beginning
We haven't quite finished our first print, because we didn't have time to calibrate the printer yet. But we sure learned a lot from just unboxing, assembling and getting the tools working.
I hope you enjoyed this writeup and hopefully we'll have our first print soon!